News & FAQs
Frequently Asked Questions
Commercial?
Our machines’ delivery lead time is different depending on the size and complication of the project. It could vary from 2 months to 5 months.
Our Machines are made to customer’s specific needs, also some project or profiles could be very difficult and new to us. We need consider extra cost
Due to our machines are custom made. It means it would be very difficult to sell to the next customer, if something goes wrong. So currently we are cautious about credit option.
Yes, we charge for services from time to time. Except outlined in the contract terms. Our service rates are transparent and will keep you posted.
Yes because our Machines are made to customer’s specific needs, our usual downpayment rate is 30% of contract value.
Technical?
The machine utilizes a series of rollers to gradually bend and form the metal into the desired shape. Each roll performs a specific shaping operation, resulting in a continuous profile.
Factors include material compatibility, desired profile complexity, production speed, and customization options. Additionally, consider the machine’s reliability, ease of maintenance, and cost.
Yes, many roll forming machines are designed for customization. Tooling can be adjusted to produce a wide range of profiles, making them suitable for various applications.
Regular lubrication, inspection of rollers and tooling, and addressing any wear or misalignment issues are key maintenance steps. Following the manufacturer’s guidelines is essential.
Operators should receive proper training, use personal protective equipment, and follow safety guidelines. Emergency stop mechanisms and proper guarding should be in place to prevent accidents.
What's new?
Rolling Process Of Roll Forming Machine
Rolling Process Of Roll Forming Machine
Cold rolling is a metal processing method at a temperature below the crystallization temperature, i.e., metal processing at normal temperature (Tcan Tktl ). The product of cold-rolled steel has a thickness ranging from (0.08 1.0)mm.
Compared to hot rolling, cold rolling has the following characteristics:
The technological process of cold rolling is much more complicated, it includes many stages from preparation of the blank to refinement and requires many complex equipment.
Due to the large deformation resistance of metal in a cold state, it consumes a large amount of energy (force F, rolling torque M, engine power P). Friction between the rolling material and the rolling axis is high, so the rolling axis surface wears quickly, requiring a special, high-wear-resistant axis.
The metal’s ability to be compressed is low, thus resulting in low productivity.
Cold rolling causes metal grain to fracture, and crystal lattice to become distorted, resulting in increased metal strength (hardness). Depending on the degree of increase in hardness of each material, each metal can only be cold-rolled to a certain degree of thickness reduction. If we continue to roll beyond that, cracks, fractures, and breaks will occur in the rolled sheet. To overcome this, we perform intermediate annealing to restore the original mechanical properties. However, it must be done within a certain thickness range that the machine can handle.
When rolling, the generated stress must be much lower than the allowable yield strength of the material axis.
To achieve high quality and mechanical properties of cold-rolled sheet products, the technology must be carried out with strict procedures, good equipment, and high-precision machine operation with minimal vibration.
The mechanical and physical properties of the metal after cold rolling increase because the mechanical and physical properties of the metal change when cold-rolled, and the metal organization before deformation has a form of grains, meaning the metal has isotropic properties (all properties in all directions are the same).
However, after deformation, the grain structure is broken, elongated in the rolling direction, and has a fiber-like or filament-like form, meaning the metal has anisotropic properties (properties in different directions are different).
4. The operating principle of roll forming machine
As a model machine, it can only roll 3-wave steel, so we use cut steel sheets. The initial flat sheet is fed into the guide table and then pushed to the pair of driving rollers. This is the initial feeding mechanism often made of 2 circular shafts with a diameter of 40, covered with rubber. When it is necessary to create pulling force, the flat sheet is inserted into the gap between the 2 shafts (the lower shaft is the driving shaft), adjusting the gap will create a pressure from the upper shaft down.
Thanks to the friction between the 2 rubber rollers and the sheet, the sheet is driven through the first rolling pair, the lower shaft is fixed, while the upper shaft is mounted on a sliding plate in a U-shaped groove on the machine body for adjusting the gap between the 2 shafts to ensure that the gap is the most reasonable. After passing through the rolling system, the product is formed with waves as required.
Operation and maintenance of the machine:
Only trained workers are allowed to operate the machine.
Before operating, check the safety systems such as the covers of moving parts, electrical safety conditions such as voltage, fuses, relays, wires…
Perform lubrication and maintenance before each shift and clean the machine before starting work.
Before putting the machine to work (with load), run the machine without load from 1 to 3 minutes to check the transmission parts.
5. Benefits of using a roll forming machine
Roll forming machine not only increases productivity but also saves costs for businesses. With advantages such as high rolling speed, high productivity, automation, the machine provides practical benefits:
Ensuring that the roll forming machine is rolled according to customer requirements, thereby increasing customer trust and revenue for the business. The machine can roll sheets of different thicknesses, colors, and materials according to customer orders.
Helping businesses save labor and insurance costs: The cost of a sheet metal rolling machine is reasonable, fully automated, and does not require many labor resources to operate.
Helping businesses save on maintenance and repair costs: If a good quality sheet metal rolling machine is purchased, it can significantly reduce maintenance and repair costs, thereby increasing productivity.
Saving costs leads to reduced prices, increasing competitiveness in the market.
The machine usually runs stably for many years, so businesses do not have to plan for frequent replacement
6. Choosing a suitable roll forming machine is a prerequisite
Currently, there are many types of metal sheet rolling machines available on the market, and selecting the most suitable one for a company’s production model is still a question that many investors are concerned about.
6.1. Choosing a rolling machine based on the practical needs of the company
The first thing to consider when choosing a metal sheet rolling machine is to calculate the actual production needs of the company, as each sheet production unit will have different customer segments, and each customer segment will correspond to the use of different types of sheets.
Choosing the most suitable metal sheet rolling machine for the production needs will help the company optimize the investment cost of machinery, save labor costs, and save production costs.
The questions to be asked are:
• What type of roll forming machine should be chosen to fit within the given workshop area?
• What is the maximum and minimum length and width of the sheet that can be produced?
• What is the material being processed?
• What is the thickness of the sheet tole?
• Is the price of the metal sheet rolling machine suitable for the financial capacity of the company?
Based on this information, the supplier will advise the customer on the most suitable and cost-effective metal sheet rolling machine.
6.2. Choose a reputable supplier of rolling machines with a well-known brand on the market
In addition to the issue of usage needs, the brand of the rolling machine is also a significant factor influencing the investment decision of most customers when choosing. When companies introduce good product lines to the market along with favorable pricing policies and good after-sales service, they will build a reputation and brand for their products.
Therefore, choosing a product based on the brand is not just following the majority, but it is also based on the experiences of other investors who have purchased and used the product and left a good impression about it. This is something that investors evaluate the quality of the rolling machine.
6.3. Consider the after-sales service and warranty of the supplier
Finally, a crucial factor that customers need to pay attention to is the after-sales service and warranty of the supplier. Vietsteel Machinery Co., Ltd understands that for technical machinery products, after-sales service and post-sale care are essential. Installation or repair, and warranty services are carried out by a team of knowledgeable, experienced, and enthusiastic staff. Vietsteel commits that when the machine has any problem, the technical team will be present promptly to avoid affecting the production progress of the factory.
How Roll Forming Machines Work
A roll forming machine (or metal forming machine) fabricates specific configurations out of long strips of metal, most commonly coiled steel. In most applications, the required cross-section profile of the piece is specifically designed for the machine to bend the metal as necessary. Other than roll forming, these machines perform a number of metalworking duties, including material cutting and roll punching.
Roll forming machines, for the most part, work in a continuous cycle. The material is fed into the machine where it continuously makes its way through the stages of each operation, ending with the completion of a final product.
How Roll Forming Machines Work
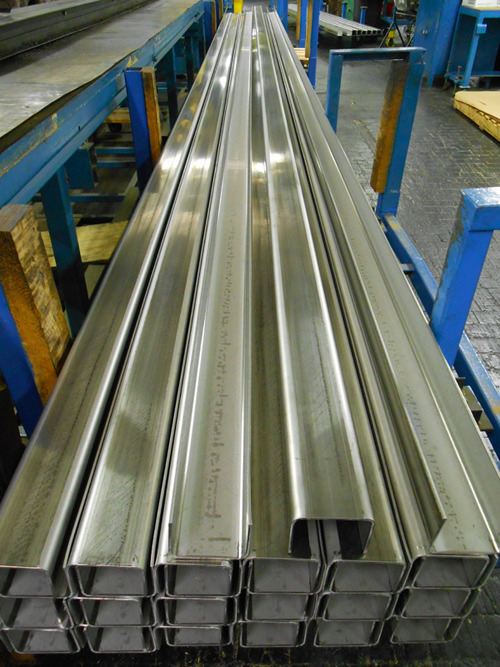
Image Credit: Premier Products of Racine, Inc
A roll forming machine bends metal at room temperature using a number of stations where fixed rollers both guide the metal and make the necessary bends. As the strip of metal travels through the roll forming machine, each set of rollers bend the metal a little more than the previous station of rollers.
This progressive method of bending metal ensures that the correct cross-sectional configuration is achieved, while maintaining the cross-sectional area of the work piece. Typically operating at speeds between 30 to 600 feet per minute, roll forming machines are a good choice for manufacturing large quantities of parts or very long pieces.
Roll forming machines are also good for creating precise parts that require very little, if any, finishing work. In most cases, depending upon the material being shaped, the end product features an excellent finish and very fine detail.
Roll Forming Basics and the Roll Forming Process
The basic roll forming machine has a line that can be separated into four major parts. The first part is the entry section, where the material is loaded. The material is usually inserted in sheet form or fed from a continuous coil. The next section, the station rollers, is where the actual roll forming takes place, where the stations are located, and where the metal shapes as it makes its way through the process. Station rollers not only shape the metal, but are the main driving force of the machine.
The next section of a basic roll forming machine is the cut off press, where the metal is cut to a pre-determined length. Due to the speed at which the machine works and the fact that it is a continuously working machine, flying die cut-off techniques are not uncommon. The final section is the exit station, where the finished part exits the machine onto a roller conveyor or table, and is manually moved.
Roll Forming Machine Developments
Today’s roll forming machines feature computer-aided tooling designs. By incorporating CAD/CAM systems into the roll forming equation, machines function at their maximum potential. Computer-controlled programming provides roll forming machines with an internal “brain” that catches product imperfections, minimizing damage and waste.
In many modern roll forming machines, programmable logic controllers ensure accuracy. This is vital if a part needs multiple holes or needs to be cut to a specific length. The programmable logic controllers tighten tolerance levels and minimize accuracy.
Some roll forming machines also feature laser or TIG welding capabilities. Including this option on the actual machine results in loss of energy efficiency, but removes an entire step in the manufacturing process.
Roll Forming Machine Tolerances
Dimensional variation of a part created through roll forming is based on the type of material used, the roll forming equipment, and the actual application. Tolerances can be influenced by varying metal thickness or width, material springback during production, the quality and wear of the tooling, actual machine condition, and the experience level of the operator.
The Benefits of Roll Forming Machines
Aside from the benefits discussed in the previous section, roll forming machines offer the user some specific advantages. Roll forming machines are energy efficient because they do not expend energy to heat material—the metal shapes at room temperature.
Roll forming is also an adjustable process and is applicable to projects of varying time duration. Additionally, roll forming results in a precise, uniform part
Training of roll forming machine
Training of roll forming machine operators can vary depending on the specific machine and the level of expertise required. However, here are some general steps that can be followed to train operators of roll forming machines:
Safety Training: Ensure that operators are familiar with the safety procedures and precautions specific to the roll forming machine. This includes learning about the machine’s operation, controls, and any potential hazards that could arise during operation.
Machine Operation: Operators should learn how to operate the roll forming machine effectively and efficiently. This includes understanding the controls and settings, adjust the machine to produce different shapes and sizes of metal parts.
Quality Control: Operators should understand the quality standards and specifications for the parts produced on the roll forming machine. They should also learn how to inspect the parts for any defects or imperfections and take corrective actions if necessary.
Troubleshooting: Operators should be able to troubleshoot common problems and malfunctions on the roll forming machine. They should know how to identify issues with the machine’s operation or performance and take appropriate action to resolve them.
Maintenance and Repair: Operators should have a basic understanding of the maintenance and repair procedures for the roll forming machine. This includes learning about regular cleaning and lubrication, replacing worn parts, and following any manufacturer’s recommended maintenance schedule.
It is important to note that training can vary depending on the specific roll forming machine and the experience level of the operator. It is recommended to consult with the machine’s manufacturer or a trained professional for detailed training on specific roll forming machines.
Basics about roll forming machine technology
What is Roll Forming?
Roll Forming is a metal processing technique that involves bending and straightening operations to shape metal sheet into desired shapes and sizes. In the Roll Forming process, metal sheet passes through a series of rolling or bending wheels to undergo plastic deformation and ultimately achieve the desired product.
What materials are suitable for Roll Forming?
Roll Forming is mainly suitable for light to medium thickness metal sheet, such as low carbon steel, stainless steel, aluminum sheet, etc. The process parameters and equipment requirements for different materials.
What are the advantages of Roll Forming?
Roll Forming has the following advantages:
Continuous mass production for improved production efficiency;
Processing of complex shapes to meet different application needs;
High precision and quality control through adjustment of process parameters and equipment parameters;
Effective reduction in production costs and improvement in product competitiveness.
What are the application areas of Roll Forming?
Roll Forming is widely used in the construction, automotive, home appliance, electronics, furniture, sports equipment industries. For example, in the construction industry, it is used in door frames, guardrails, stair railings, etc.; in the automotive industry, it is used in door panels, roofs, chassis components, etc.; in the home appliance industry, it is used in refrigerators, washing machines, air conditioner housings, etc.; in the electronics industry, it is used in circuit boards, electronic component housings, etc.; in the furniture industry, it is used in chair legs, table legs, etc.; in the sports equipment industry, it is used in bicycle frames, ski boards, etc.
What are the basic steps of Roll Forming?
The basic steps of Roll Forming include metal sheet leveling, trimming, feeding, bending, straightening, and cooling. In each step, precise control of process parameters and equipment parameters is essential to ensure the quality and precision of the final product.
Why choose us? About